Bearing Application design and selection
MDM Engineered solutions can provide expert solutions for bearing applications were “off the shelf” solution have failed. There are many examples of solved challenges that Voya had encountered in his professional life.
Below is an example were a split vertical housing had to be designed and manufactured to solve an ongoing problem. A client had a Dryer section that used friction bearings. These were quite old, and one of the shortfalls was that the lubricating oil was getting to the product. The decision was made to replace these bearings with spherical roller bearings. However there were some restrictions that were making this job a unique one and worth mentioning. First, the shaft was recessed at the bearing seat, making it impossible to mount an ordinary bearing. The use of a split bearing was obvious, but the customer was not ready to accept the cost of a spilt bearing in multiple locations in the dryer. The second problem was that the center distance between the bearing center and vertical support beam was very small, and “off the shelf” vertical housings could not be used. A third problem was that the “off the shelf” housings had a split at 45°, and our customer requested a split that would be horizontal. A requirement for effective seals was a must heaving in mind the experience with the previous bearings. This was an interesting challenge so I decided to take it on.
In order to solve the first problem (recessed shaft) I decided to make a split adapter sleeve that would fit on the recessed part of the shaft and therefore allow the bearing to “jump” over the non-recessed part of the shaft while being mounted. FAG will manufacture the split adapter with the 8” bore. The bearing would be an ordinary spherical roller (FAG 23048K.MB) with a taper bore. As the recessed part of the shaft was quite larger than the bearing and adapter length through the bore, and the baring needed a shoulder, I designed a split spacer that was held in place by a sleeve. This sleeve was also used as a running surface for one of 4 split seals used The second problem and the third one were solved commonly by implementing the horizontal split of the housing and bolting the top half of the housing to the back mounting plate, something that was not done before. The seals were designed in a way that their inspection was possible at any time without opening the housing.
Here is a 3D model of the housing only (without the bearing, adapter and seals) created in Solid Works 2004:
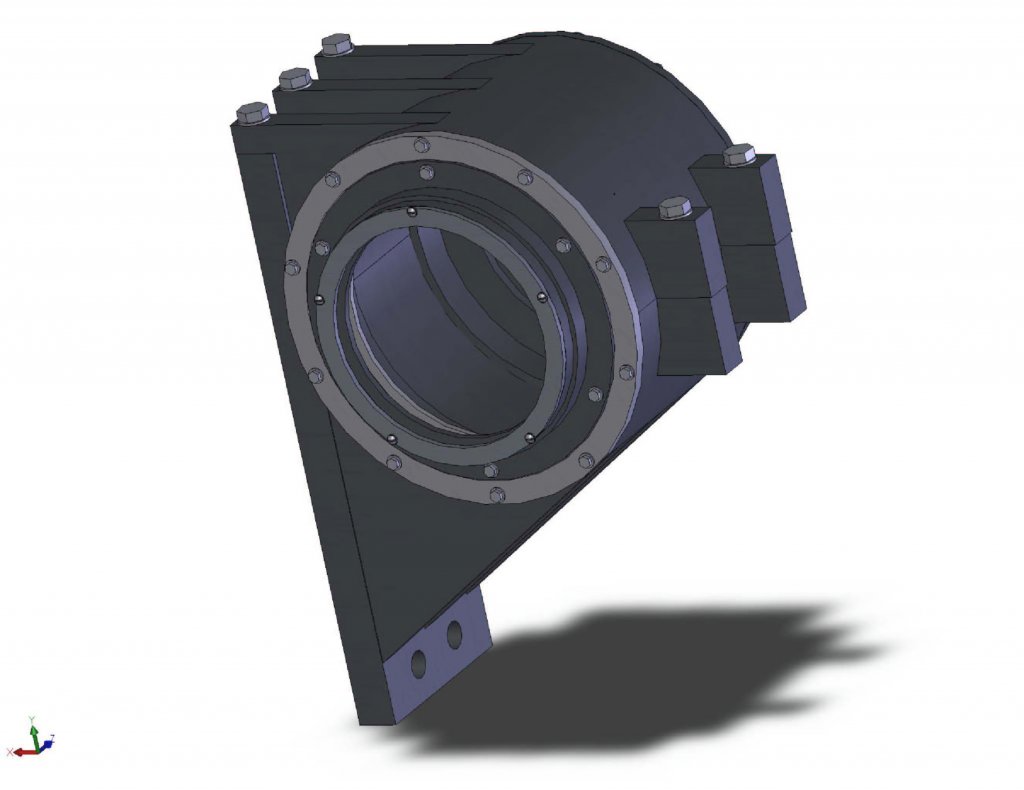
Here are the original drawings (Auto CAD) of the cross section and the side view of this housing:
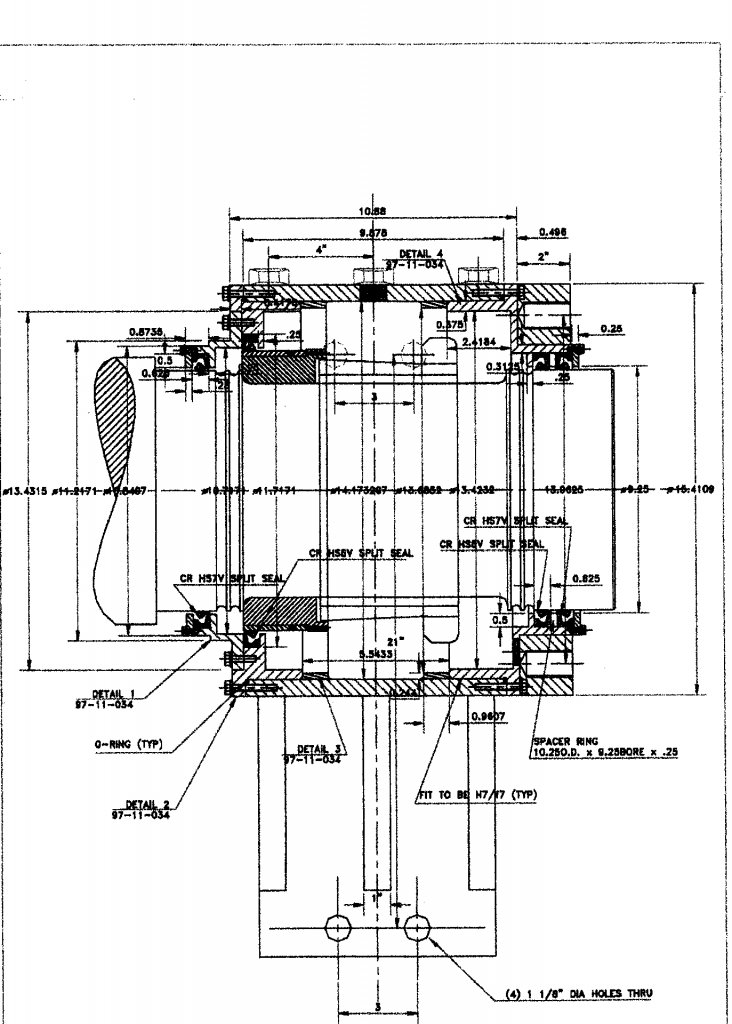
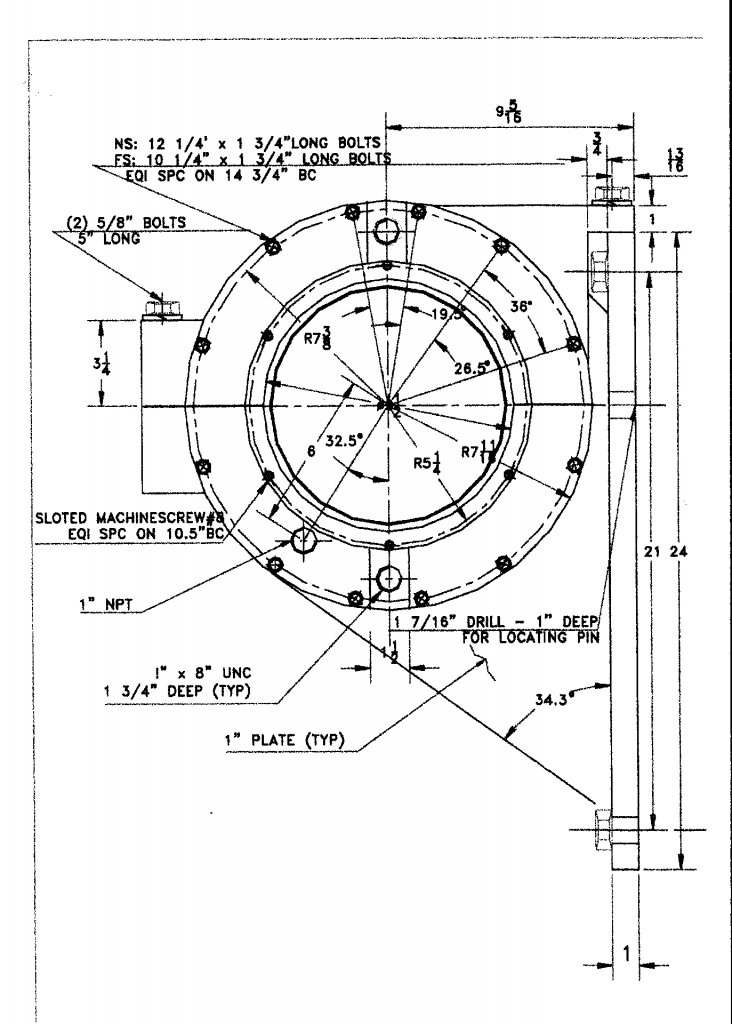